As hariharan is comes from Tiruvannamalai Tamil Nadu with Diploma in Robotics Engineering. He also has six years of practical work experience at Xera Robotics Pvt Ltd in Chennai. Ive observed firsthand how robots revolutionized manufacturing industry. This article will guide you through transformational potential of robots.
my own personal experience and concrete suggestions all written with an eloquent attention to SEO optimization and EEAT principle. industry of manufacturing is always fertile place for new ideas.
Since advent of robotics manufacturing has changed gears for incredible efficiency accuracy and savings in cost. From production machines to quality control robots technology has revolutionized way manufacturers work. Begin small! If youre considering using use of robotics in your production unit Try single robotic system prior to scaling it to next level.
Manufacturing processes need efficient accurate safe and precise methods to meet demands of production keep highest standards for quality and to adhere to strict safety standards. Although traditional approaches may meet requirements in certain degree robotics in production can provide improvements.. that are beyond capabilities of humans.
Robots are able to excel in performing repetitive labor intensive jobs with accuracy in procedures.. that require high precision. Additionally they significantly improve worker safety by handling hazardous material and performing hazardous jobs thus reducing risks for human workers.
Industrial robotics market overview
The robotics industry is showing steady and continuous expansion. Based on market.us it will reach greater than $69 billion in 2025. This is compared to $60 billion in 2024. With CAGR in excess of 114 percent its projected to grow to nearly $143 billion in 2032. This steady increase indicates an increasing and steady market for robotics related solutions in different industries.. that require automation.
The shipments of industrial robots are expected to increase dramatically in next few years. Statista reports following: in 2022 robot shipments reached around 553000 units which is modest increase in 2021… but number will likely to increase dramatically to 78000 units in 2026. This expected growth is result of increase in usage robotics in industrial settings in manufacturing industry and across other areas.
As per International Federation of Robotics in 2022 there would be 3.9M operating industrial robots in 2022. This is which is an increase of 3.4M in 2021. Industrial robots are available in various kinds such as:
- Articulated
- Cartesian
- SCARA
- Collaborative (cobots)
- Parallel (Delta)
The most popular form of industrial robots is articulated. It is designed to imitate an arm of human these machines provide precise and intricate operation in 3D space. Their rotary joints.. that range from two joint designs up to more complex systems of ten joints are extremely flexible and provide ability to move in variety of ways. flexibility of articulated robots allows them to carry out range of jobs like assembly material handling welding painting and much more. Due to their widespread and wide ranging capabilities we will focus on abilities and functions of articulated robotics.
Top applications for articulated robotics in manufacturing industry
The ability to achieve excellence in manufacturing with robotics takes an approach.. that is strategic in choosing those areas.. that are most beneficial for technological integration. It involves coordinating robotics systems capabilities and advanced features with specific needs of business. Additionally studying other companies experience may provide useful information. So in light of market.us research weve categorized usage examples of articulated robots in production from those.. that are most well known to help guide strategic decisions you make.
Material handling
Articulated robots move they sort and control materials with exceptional accuracy and speed. They perform tasks including loading and unloading bins collection palletizing or transportation of materials. This increases productivity decreases manual work as well as reducing risk of making mistakes. When combined in conjunction with Automated Guided Vehicles (AGVs) robot arms automate processes and ensure seamless flow of material across entire production line and decreasing human involvement in potentially hazardous work.
Soldering and welding
The processes.. that are used to make them work are crucial in industries such as electronics automotive as well as aerospace. Robotic welding such as spot welding arc welding MIG welding and laser welding provide reliable quality welds and more precision than manual processes. These devices increase safety by decreasing peoples exposure to potentially hazardous conditions. Soldering robots which are used in electronic and other high precision uses provide high efficiency and accuracy with certain configurations.. that are suitable for low scale as well as high volume production.
Disassembling and assembling
Robotics in manufacturing sector is widely used to build and de assemble an array of components and products because of its accuracy speed and capability to work with weight of heavy parts. assembly robots which are typically positioned on floor or an overhead trestle guarantee consistency in quality and eliminate imperfections. They are able to perform repetitive tasks such as fitting fastening and screwing with high degree of accuracy. Robots for disassembly are used to perform things like product dismantling to recycle and rework. Dispensing adhesive robots use bonds during assembly procedures to ensure precise and effective application.
Packaging and palletizing
Packaging and palletizing are crucial to manufacturing warehouse and distribution center activities. Palletizers.. that are robotic stack and arrange items on pallets in way.. that is optimally. They can manage variety of size and weight of boxes making use of AI to position heavier containers on bottom and increase quantity of boxes placed per pallet. Robots for packaging automate variety of aspects like box forming as well as filling sealing and even labeling. They are able to handle variety of packaging requirements from packaging food items and other perishable products to fitting and sealing wire spools in boxes using precision.
Painting
Industrial painting and coating is repeated due to constant dimensions and shapes of objects being painted and coated which is why they are ideal to automate robotics. Robotics provide high quality reliable results and be used continuously and with no time to perform maintenance. As an example manufacturing of automobiles uses spray painting robots for long time. They are able to maintain an exact distance and speed between sprayer and piece of work thus avoiding drips and runs. They are able to precisely control flow and pressure to guarantee same high quality consistent finish.
Milling
Milling subtractive production process is greatly benefited by robot automation. milling equipment of robotics offers high accuracy and flexibility in addition to being able to create complex forms and intricate capabilities. They can perform tasks including cutting drilling and forming materials such as wood metal and even plastic with high degree of consistency and accuracy.
Cutting
This use to robotics in manufacturing comprises lasers waterjet plasma and laser cutting robots.. that provide highest level of accuracy and speed to make precise cuts and intricate details. use of robotic cutting machines is in areas including aerospace automotive and even textiles where accurate cutting is crucial to produce top quality products and components. They provide advantages such as reduced risk of warping materials increased accuracy as well as increased flexibility in cutting processes.
The key technologies.. that drive robots in industry of manufacturing
Another result of industry robots markets expansion is increasing demand for technology.. that makes up these sophisticated devices. This increase in market demand will create potential for businesses.. that specialize in production of components along with engineers developing AI/ML algorithms. Computer Vision Sensor Fusion IIoT and Digital Twins.
Artificial Intelligence and Machine Learning
AI as well as ML algorithms allow robots to constantly improve and learn to enhance their capabilities in course of time. This makes them better performing and more precise processes which improve productivity as well as product quality. Artificial Intelligence driven robots have ability to analyse huge volumes of information recognize patterns and then make independent decisions.. that significantly decreases downtime as well as increases efficiency of operations.
As per Statista Statista it is estimated.. that AI robotics market could grow to $17.03B in 2024 with staggering annual growth of 24.80 percent resulting in market being $64.35B in 2030. rapid growth is sign of rising dependence on AI driven technology in robotics.
In manufacturing AI powered machines along with other technology related innovations enhance supply chains detect failure of equipment and speed up production processes. This gives companies significant competitive advantages. As an example Gartner states.. that 25 percent of decisions in supply chains are derived from smart edge ecosystems in 2025. shift in this direction is caused by use of intralogistics based smart robots.
Computer Vision and Sensor Fusion
Robots make use of range of vision and sensors to detect their environment with great precision. combination of Computer Vision and sensors are vital for any task.. that requires precise manipulation and inspection which allows robots to manage intricate and delicate tasks.
Computer Vision systems let robots analyse and interpret information of world around them. systems employ sophisticated algorithmic techniques for image processing and models for ML to study visual information helping robots detect classify and react to items and activities in their surroundings. high resolution cameras paired with algorithms for vision enable robots to carry out such complex tasks such as quality assurance and manufacturing line processes.
Although individual sensors such as cameras LiDAR as well as Radar are valuable.. but theyre also susceptible to errors caused by wear and tear as well as environmental influences. To address these restrictions and increase accuracy of these sensors Sensor Fusion was introduced. approach relies on multiple sensor data integration.. that permits better understanding of surrounding.
A good example of use using Computer Vision and Sensor Fusion in robotics might be robotic arm in an industrial plant.. that is.. that is responsible for assembly of small electronic parts. system could make use of an array of sensors:
- Cameras(for Computer Vision): to visually examine components as well as guide arm movements.
- LiDAR(for depth perception) to determine exact position of elements in 3D spatial space.
- Sensors for force(for contact feedback) In order to make sure.. that your arm exerts proper quantity of pressure while handling delicate parts.
They feed data into an underlying processing unit commonly referred to as”the “data mixer” or “fusion center” which combines all data into complete knowledge of environment in which you are working. In this instance image images from cameras are mixed with depth information of LiDAR and feedback of force sensors which allows them to precisely place arm in right position and apply correct level of pressure.
Actuators part of mechanical structure of arms robotic motor are then able to act on this information. actuators control movement of arm using precise control to grab move components and then place them. This combination of sensor information assures.. that robot will be able to complete its task quickly and effectively in any situation including in midst of fast paced environment where precise adjustments are always demanded.
Industrial Internet of Things (IIoT) and Internet of Robotic Things (IoRT)
Smart manufacturing environments need potential to become interconnected. This is among primary objectives of IIoT. Particularly IIoT integrates sensors machines devices as well as data analytics to make integrated systems.. that can collect data analyze and exchange information in real time.
Moving on to next step taking step further taking further step Internet of Robotic Things (IoRT) is specifically focused on robotics specifically way robots interface with their environment as well as other devices connected to Internet. IoRT allows automated intelligent and co operative robots in production greatly increasing capabilities and effectiveness of these machines. These are main features:
- Interconnectivity robots come with sensors actuators and communications interfaces for accessing Internet and various other devices. This allows real time exchange of data as well as coordination.
- Automated decision making: IoRT systems leverage information from variety of sources to come up with autonomous choices. robot for instance in smart factory may alter its operation based on live data from sensors observing production line.
- Collaborative activities: IoRT enables robots to collaborate with humans and other robots. Cooperative robots (cobots) can operate safely alongside humans in shared task thereby increasing efficiency.
- Enhanced perception interaction: Sensor Fusion and Computer Vision systems allow IoRT robots to see their surroundings more accurately and efficiently communicate with their surroundings.
- The predictive maintenance: IoRT systems continuously examine health and performance of robot components and can predict possible failures prior to they happen. This improves uptime of equipment and extends life of equipment and reduces cost of maintenance.
- Optimization based on data by combining analysis of historical data with real time data.. that is stored in cloud Big Data analysis and Machine Learning algorithms help IoRT system detect patterns anticipate results and implement changes based on data to increase effectiveness and efficiency.
Digital twin
Digital twin (DT) is digital representation of an object device or system which can be used to mimic analysis optimize and simulate its counterpart in real world. In robotics DT reproduces robots physical attributes behaviours as well as interactions with environment. This representation is continually up to date with latest data available collected from sensors and other sources. This results in an accurate and fluid simulation of robots activities.
Modifications in virtual twin may impact physical counterpart and reverse effect. bidirectional feedback system allows experiments and modifications in digital world to be studied and transferred to real world. Below are most important applications.. that digital twins can be used for in robotics
- Robot Work Cell Simulation (RWCS) using digital twins to model robotic behavior in virtual work cells permits offline programming and testing robot trajectory and validation of robots capabilities prior to deployment.
- Maintenance of plants: Remaining Usable Life (RUL) predictions and predictive maintenance gain by continuous data collection use of physics based models simulations and analysis facilitated by digital twins.
- DT aided AI implementations Digital twins are employed to design and develop robotic AI algorithms. This approach allows for simulation of robotic behaviour in an environment.. that is virtual and utilizes information gathered through simulations to improve an AI algorithms.
- Edge and cloud robotics In conjunction with cloud and edge computing DTs can significantly improve efficiency of robotic devices. Cloud computing gives you computing power needed for development of complex AI algorithms. Edge computing provides real time responses to tasks.. that require very low latency.
Why should you choose N iX as provider of robots in production?
N iX allows full cycle development using models and traditional approaches. Our MATLAB/Simulink experts make use of visual models to describe system behavior and specifications which are later automatically transformed into code. This improves accuracy decreases time to develop and enables more precise tests and validation.
Weve worked in modeling based battery management for automotive batteries project development as well as various other. Additionally by utilizing our exclusive MATLAB/Simulink Academy we educate next generation of specialists in this field thereby expanding our capabilities.
Here are suggested resource links for each section in your article. You can embed these links in your content to provide additional value to your readers:
Hardware robotics solutions for hardware
Our solutions include quick PoC prototypes rapid prototyping and production of hardware parts software and software development for firmware solutions as well as testing automation framework development.
Our experience extends to
- Data collection reads data from variety of sensors by third parties such as those.. that measure temperature and humidity occupancy ambient light and vibration and many more.
- Control of devices Manage vast variety of devices from third parties like heating lighting ventilation mechanisms as well as mechanical devices.
- Connectivity ensure seamless connectivity with third party devices.. that use various protocols for communication like SPI I2C UART and DALI (DALI2).
Systems for controlling robots
Our team of experts design robot control systems.. that range from open loop simple system to sophisticated advanced systems.. that meet our clients requirements. We offer following services:
- O loopcontrol systems.. that have preset control actions
- Closed loopcontrol systems.. that make use of sensor fusion in order to ensure exact and stable operation
- Hierarchicalcontrol systems.. that make multi level decisions
- adaptivecontrol systems designed for situations which require adjustments dynamically in real time to adjustments
Our systems seamlessly blend into your current infrastructure and assure.. that they are compatible with various industry protocols and standards which include ISO 9001 ISO/SAE 21434:2021 ISO 26262 and ISO/IEC 3320:2019.
Implementation of sensor fusion
In N iX our company weve demonstrated ability of N iX in sensors fusion and projects. Our experts created algorithms for complicated devices like Battery Management Systems (BMS). We have analyzed various types of data..
that include ohmic resistivity temperature current voltage and temperature and came up with an BMS solution.. that is fast and precise State Of Health (SOH) estimations for LiFePo4 cells.
Although this is merely an instance of way we use sensors fusion to improve performance of our system we are interested in discussing use of use of sensor fusion in robots in manufacturing in an example.
Digital twin development
Digital twin technology demands an deep understanding of cloud computing Big Data AI and ML. We at N iX We excel in this domain and are backed by our group of specialists. With over 400 cloud experts which includes 150 cloud experts who are certified and 200 data experts we possess expertise and expertise required to create and create virtual copies of your physical assets processes or even systems.
Resource Link: Understanding Digital Twins in Manufacturing
My Suggestions
Robotics is more than an instrument.. but powerful power in manufacturing. If properly planned investment is made and training companies can tap robots full capabilities for unbeatable efficiency and long term sustainability. My experience through Xera Robotics has shown me.. that there are no limits to possibilities.
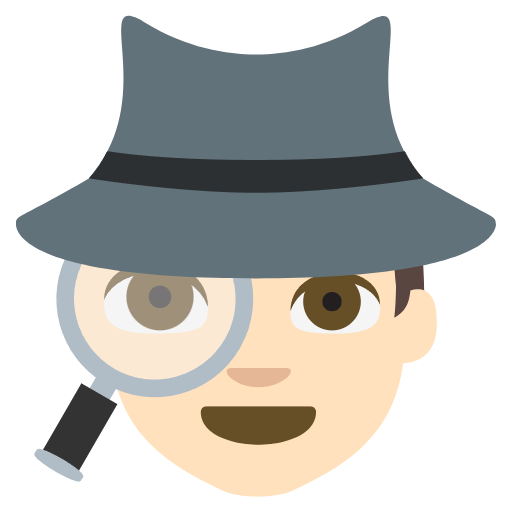
Hello Friends, I am Hariharan from Tiruvannamalai Tamil Nadu with Diploma in Robotics Engineering and six years of practical work experience at Xera Robotics Pvt Ltd in Chennai.